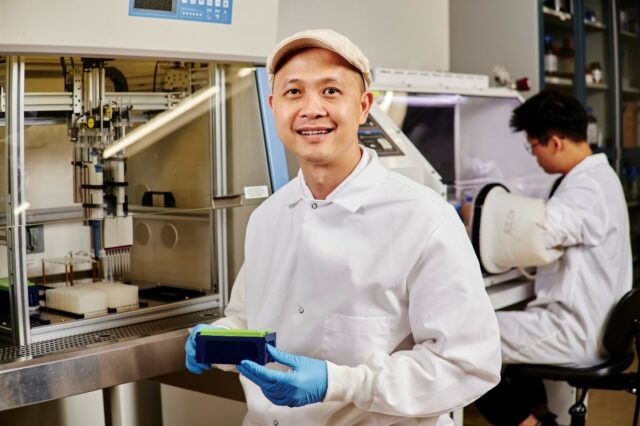
Researcher Cong Trinh of the University of Tennessee Knoxville uses a liquid-handling robot that allows high-throughput screening for enzymes. Credit: Cong Trinh/University of Tennessee
Recent research coordinated by the Center for Bioenergy Innovation paves the way for creating biofuels made by microbes with greater speed, efficiency and flexibility. The effort led to major breakthroughs described in a study published in July in Metabolic Engineering.
Over three years, a team of scientists designed specialized enzymes that trigger bacteria to manufacture compounds called esters. Esters can be used in biofuels, fragrances and flavors.
A specific bacterium that is a specialist at degrading crop waste, grasses and wood was chosen as a platform to turn these feedstocks into specific esters for use as clean fuel. However, the class of enzymes that trigger this change – known as alcohol acyltransferases – had never been known to function at the high temperatures the bacteria required. To tackle this problem, the team searched plants, bacteria and fungi for related enzymes that operate at high temperatures, tweaked their components, and plugged them into the bacteria.
The research was led by Cong Trinh, an associate professor of chemical and biomolecular engineering at the University of Tennessee in Knoxville, who collaborated with partners at the Department of Energy’s Oak Ridge National Laboratory and the Joint Genome Institute, a DOE Office of Science user facility.
The Joint Genome Institute assisted with synthesizing gene sequences to make the enzymes, identifying which work best for creating particular esters. After the research team manipulated the enzymes and tried out different gene combinations, ORNL staff scientist Richard Giannone analyzed the productivity of the genetically-engineered enzymes.
Trinh said the team was able to create enzymes that made large amounts of various “designer” esters, with few byproducts. These enzymes worked in various microbe hosts, using a variety of pathways. And they could function even in unstable conditions, such as temperatures above 55 degrees Celsius, or 131 degrees Fahrenheit. This flexibility makes the enzymes compatible with more host microbes and more practical for industrial-scale manufacturing.
“Before our work, there was no report at all of natural enzymes that can work at high temperatures like this,” Trinh said. “The enzyme we engineered can make up to 160 unique molecules of esters, possibly more.”
Potential uses for these esters extend beyond biofuels. For example, because esters define fragrance profiles, some of the esters developed could be used to make crops more attractive to pollinating insects, Trinh said.
The research team has already published further results in Metabolic Engineering and Biotechnology and Bioengineering as they hone ways to speed up the enzyme engineering process.
“Now that we understand how to manipulate the enzymes, we develop ways to characterize them rapidly and engineer them rapidly,” Trinh said. “This allows us to ‘plug and play’ for different microbes, to make different types of esters we are interested in. We can make different products without having to go through the process of re-engineering for different uses.”
Trinh said that’s a key step in rapidly scaling up the technology for biofuel production to replace petroleum fuels, which is vital in reducing greenhouse gas emissions and addressing global climate change.
The Center for Bioenergy Innovation (CBI) at ORNL is one of four DOE Bioenergy Research Centers focused on advancing biofuels and bioproducts for a vibrant domestic bioeconomy. CBI is accelerating the development of bioenergy-relevant plants and microbes to enable production of drop-in sustainable aviation fuel, bioproducts that sequester carbon, and sustainable replacements for plastics and other environmentally harmful products. CBI research is supported by the Biological and Environmental Research program in DOE’s Office of Science. –S. Heather Duncan